PROCESS
The Pottery Tradition
Making ceramics is as old as humankind. Potters take malleable clay, form it into shapes, dry it, fire it, decorate and glaze it, and then fire it again until it can no longer return to its malleable form, having been chemically altered by the firing. There is a huge loss ratio along the way to producing one beautiful object: pieces break or crack before firing, they warp or crack inside the kiln, the glaze fails to work as expected, or the kiln fails. As frustrating as that might sound, for me, the process of making, the repetition, the physical effort, the refining of an idea, the experimentation along the way to finding a different way to solve a problem are just plain all-engaging. I love clay!
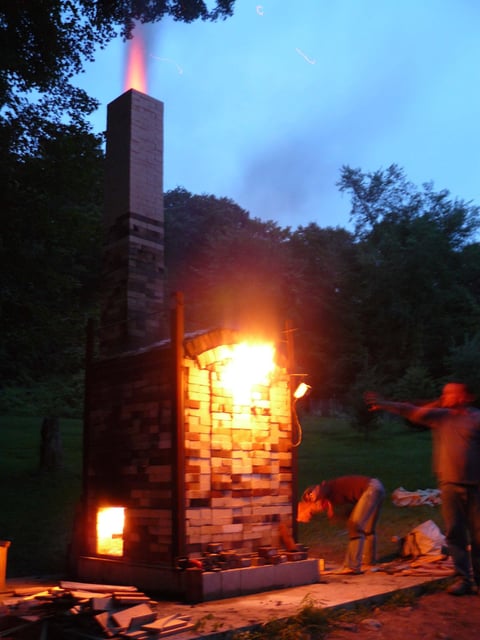
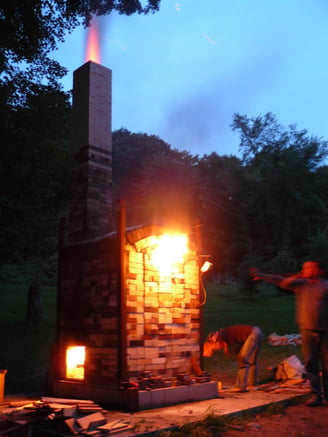
Technical Information
I work in porcelain and stoneware, usually fired to Cone 6 in oxidation. I have participated in other sorts of firings (like the wood fire kiln pictured here), some soda kilns and gas kilns and a raku kiln, but New York City is not a place for flames leaping into the sky, so I usually fire in an electric kiln in the teaching studio where I produce my work.
I used to throw most of my work on a wheel, but arthritis makes that painful, so now I concentrate on handbuilding my work the old fashioned way, one piece at a time.
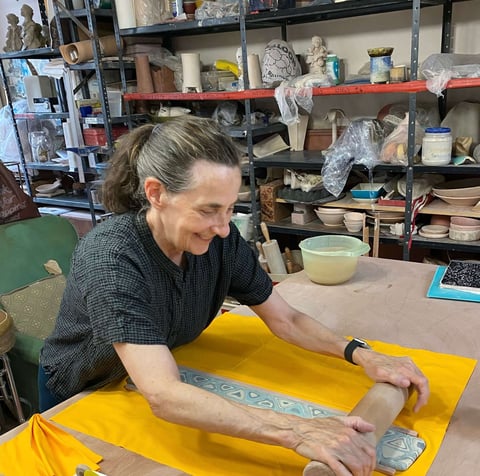
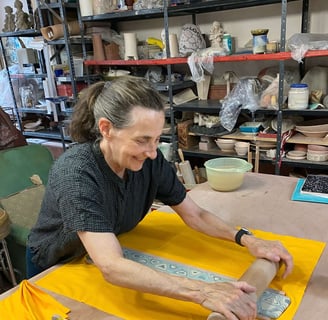
Nerikomi technique
Nerikomi is a Japanese process which involves coloring porcelain with pre-fabricated colorants (I use Mason stains) and then arranging the colored clay in patterns that are visible through and through the finished object. My favorite Nerikomi artists are Barbara Gittings and Dorothy Feibelman - look them up on Insta!